What is Total Cost of Ownership?
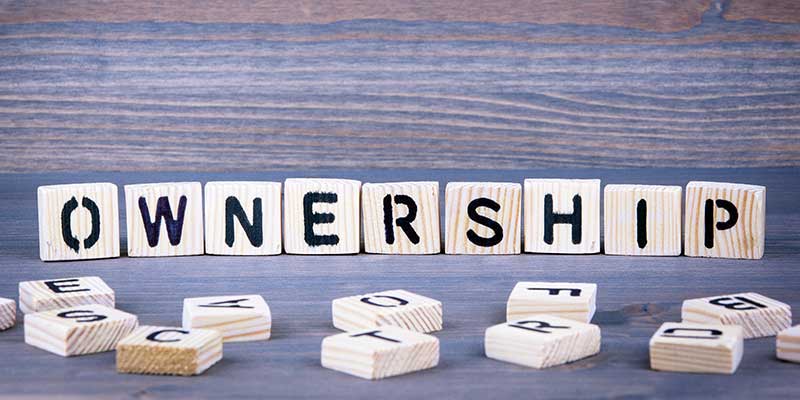
How much do you know about TCO? Are you using it to your best advantage?
For many companies, Total Cost of Ownership (TCO) has a significant influence on buying decisions and supports negotiations from customer and supplier perspectives. It allows companies to look deeper than the purchase price when deciding whether or not to buy.
At its core, TCO is a financial estimate and procedure that estimates all the costs associated with an asset. Acquisition costs are included along with every direct and indirect cost throughout the asset’s life cycle: assembly, production, warehouse, distribution, administration, and more. When you estimate TCO, you can identify known cost-drivers and hidden costs before you make the decision to invest.
The History of TCO
Different TCO procedures have been recorded since at least the 20th century. However, today’s understanding of TCO dates back to 1987, when the consulting company Gartner Group developed and promoted TCO to assess costs for IT infrastructure. In the decades since, TCO has been approved and adopted globally.
Many different methodologies and software tools have been developed to analyze TCO in a variety of different contexts and industries. No matter the methodology or the application, the goal of TCO is always to understand and reproduce the true costs of acquiring an asset.
Where can TCO be applied?
Total Cost of Ownership is very versatile. It can be used in many different contexts across different industries. Companies and individuals can estimate the TCO of any purchase that they make: anything from a person buying a new car to a large enterprise purchasing software to be used around the globe.
Bossard focuses on TCO where it applies to C-parts—screws, nuts, washers, and other small but essential parts that are handled in bulk.
Tangible Benefits of TCO
TCO helps you save time and labor costs in the following ways:
- Easier to compare different suppliers
With a TCO-based supplier evaluation system, you can measure and evaluate different supplier performances and decide which is the best fit.
- Easier to identify optimization potential
TCO can help you find potential for optimization by improving the transparency of the cause and effect chain.
- Increases cost understanding throughout the company
Breaking down the costs and sharing the information with employees allows them to understand cost optimization.
- Helps decide whether to make or buy
Evaluating the total cost of ownership is essential in making a rational choice when it comes to make-or-buy decisions.
- Helps define the economic order quantity
TCO calculations give you the basis for an economic order quantity (EOQ) evaluation, allowing you to minimize total costs of inventory.
Intangible Benefits of TCO
TCO increases organizational transparency and responsibility in the following ways:
- Improves internal corporate communication
You can base decisions on consistent data sets and clear reasoning, reducing conflict and confusion among employees and management.
- Strengthens the negotiation process
When negotiating with suppliers, you can back up your position with results from the total cost of ownership evaluation.
- Useful for product development and sales
Considering manufacturing/selling? Take a TCO perspective from the point of view of potential customers to see where you stand among the competition.
Breaking Down TCO: Cost Categories & Cost Elements
There are two levels when calculating the TCO: cost categories, and cost elements (also known as cost drivers). Depending on the case at hand, you will have different cost categories and cost elements and you may structure these levels in different ways. Common cost categories are listed below, and most cost elements will fit into one or more of these categories.
There are 6 cost categories to calculate the TCO, according to Ellram and Siferd (1993):
- Quality
Contains cost elements relating to both supplier quality and product quality
- Management
Encompasses procurement costs, leading costs, and planning costs
- Supply
Consists of goods received as well as faulty or delayed supply deliveries
- Service
Contains cost elements relating to installation, maintenance, and further services
- Communication
Encompasses both internal and external (supplier) communication costs
- Price
The most straightforward of the 6, this contains expenses like order quantity and delivery.
Problems with TCO Implementation
Even though TCO offers tremendous benefits in nearly any situation, there are issues that can come about during its implementation, especially if the concept is foreign to those within your organization.
The main problem comes about when a company tries to copy a TCO model from another company. Due to the multiple complex factors that go into a TCO evaluation, it simply is not effective to copy a model from another company. That is why we don’t include a sample model here.
There are other issues that can come about when trying to introduce TCO to a company. Employees must be educated and trained, internal operating processes may need to be changed, and conflict within the existing corporate culture may occur.
If there aren’t enough data sources and systems to help determine the cost elements, that creates another hurdle to TCO implementation. And, the time it takes to complete the total cost of ownership evaluation can be an issue as well.
Despite the issues, we believe that TCO is an important part of the decision-making process. Efforts should be made to mitigate the problems associated with TCO implementation so that your company can reap its benefits.
Learn more here and get the full E-Book now!
Sources:
Ellram, L. M., & Siferd, S. P. (1993). Purchasing: The Cornerstone of the Total Cost of Ownership Concept.