Quality assurance and flawless production quality
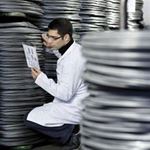
High quality starts with selecting the correct raw material. This influences most production steps, especially those that add strength to the product, such as heat treatment, which creates the basis for the correct mechanical properties when the parts are manufactured.
In theory nuts and bolts could be manufactured from pure iron. However, pure iron would be far too soft for many fasteners. In order to increase the strength, carbon is added to the molten iron at the steel works. The carbon content is a critical factor in the strength of the resulting steel. For example, a bolt of property class 12.9 needs a certain strength, and it is the carbon that gives the steel its strength after having been quenched in oil at close to 900°C.
That is why we carefully select the material for our products to ensure that it is strong enough for its application.
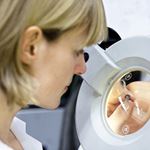
There are many methods and technologies for producing a fastener. For example, cold forming, hot forging, machining of cold drawn bars, zinc die casting and injection molding. Each of these methods has its own unique advantages and applications.
Cold forming is a common technique for bolts and screws in sizes M1 to M24 in diameter. This methodology is also used in producing nuts sized from M3 to M16. Other factors, such as the end application of a fastener, economic order volume and cost, need to be considered when selecting a production method.
No matter which production method is selected, it involves a series of production steps that have a significant impact on the quality and performance of a fastener.
At Bossard we have strict manufacturing selection criteria and in-process control.
In-process control is the most efficient way to ensure that product quality is in accordance with the requirements. Every production step is monitored throughout the production process and deviations are identified and corrected almost instantly. The result is less risk, higher quality and timely delivery.
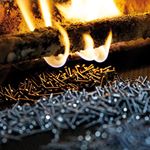
Heat treatment is one of the critical processes in making a fastener. It is a process where the physical properties of a material are changed by heating and cooling.
Metallic materials consist of crystals. Heating and cooling can manipulate the properties of the crystals and the overall mechanical behavior of the fastener. For many products, heat treatment is the only way to obtain the required mechanical properties.
Another important aspect concerning safety in fastener applications is corrosion protection, which means preventing fastener failures due to corrosion over the useful life of fastened products. Protection against corrosion can be achieved through several ways, such as a good protective design, surface coatings, or selecting a corrosion resistant material. While there are many different approaches to corrosion prevention, choosing the optimum protection requires special expertise.
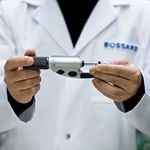
With more than 80 technical experts worldwide, Bossard ensures that correct manufacturing processes are performed. Our experts are specially trained in each and every process in fastener production.
Our team of experts comprises product, process and assembly specialists. They are highly trained in fastener production process. Most importantly they understand what every process means to your fastening application and quality requirements.
Our aim invariably is to identify the most efficient and highest-quality fastening solutions. These can be standard products or special new parts developed together with you in order to optimize production and the end product. Such comprehensive support leads to your success in the market.