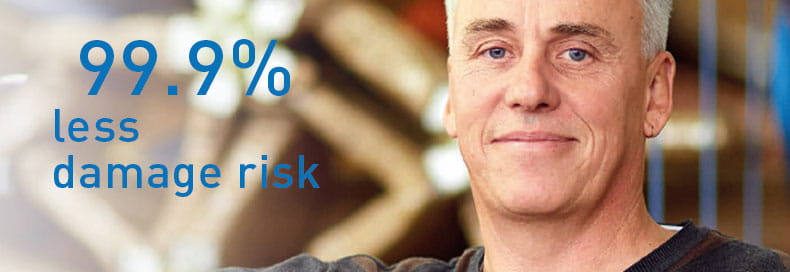
Markus Simitz, Purchasing Manager, Embru-Werke AG, Switzerland
"For a handful of screws"
Anybody who went to school in Switzerland has very likely sat on an embru chair. Forty percent of classrooms in Switzerland have embru chairs, which has a lot to do with our slogan “Furniture for a Lifetime”. But rather than advertise for embru, this is simply meant as the backdrop to illustrate how severe a problem it was a few years ago when complaints began piling up about our best-selling school chair.
How quickly could we find the solution?
The rubber caps on the feet of some chairs had been coming off in some cases. Sounds pretty harmless, but school floors are often linoleum, and linoleum floors are difficult and expensive to repair or replace. At that time we had some 50 000 of these chairs in Swiss classrooms. So every complaint was making us increasingly nervous. Where did the problem lie? And how quickly could we find the solution? An internal analysis indicated the screws might have been the problem. And under sustained force – such as when students lean back in their chairs, as they like to do – the rubber caps came off the countersunk screw. But what to do?
We wanted to replace the screws, not parts of the chairs
“Let‘s ask Bossard,” I said, because they have the equipment to test out alternative screws. After several lab tests, a Bossard engineer confirmed that the screws were in fact the problem. So together we designed a half-dozen new screw prototypes. The challenge was to ensure backward compatibility, i.e. the new screws had to be compatible with the chairs already delivered, their casters, caps and 4.0 mm screw holes. We just wanted to replace the screws, not parts of the chairs or whole chairs, which would have cost an enormous amount of money. New screw in, problem solved – that‘s how we wanted it.
After three weeks of testing Bossard did in fact deliver “our” screw. It was not cheap of course, but what do a few high-quality screws cost compared to replacing a linoleum floor and our customer service having to resolve warranty claims?
We further use a high precision computerized screwdriver that was strongly recommended by the engineer, which actually cost more than the screws. The force is just as important as the screws themselves, he had told us. The screws would be too loose or overtightened if there were more than minimal torque differences.
But now we have peace of mind. Complaints have virtually ceased, and when one is received, we know what to do. So that‘s what comes of partnering with Bossard. We functioned as a team. It saved us a lot of money, and what is nearly more important, it raised our awareness that solutions to design problems can often be found in fastening technology, such as the right choice of screw. This insight is already helping us with new designs.
Ref. BOS-AE-OT-00514
AcceptReject