EV OEMs face challenges due to fragmented production processes, where design and assembly are their responsibility, but manufacturing is handled by a tier supplier. This often results in costly trial and error approaches, leading to poor product quality and high maintenance costs for end-users. A familiar situation also for a leading truck manufacturer. Collaborating with the OEM designer and tier supplier manufacturer, Bossard developed an insert-stud solution for an EV battery application, that addresses stakeholder requirements, ensuring precise design fit, electrical performance, and assembly loadability.
Meeting the challenge of tight clearance
In vehicle battery and electrical systems design, minimizing weight and space utilization leads to thin materials and tight spaces. Multiple components, wiring, connectors, and busbars must fit within geometries that push polymer molding design rules to the limit. However maintaining intercomponent spacings and clearances is crucial for reliability in harsh operational conditions, e.g. to avoid short circuit. Molding these complex arrangements often requires complex tooling, making conventional fastening solutions impractical.
Against this backdrop, Bossard designed an insert stud fastener for securing electrical components onto a polymer carrier, ensuring a fit within the myriad packaging and electrical isolation constraints, while respecting polymer molding design requirements, and thus facilitating a viable mold solution.
Understanding the material and processes
Polyamides like PA6 and PA6.6, reinforced with glass fibers, are versatile for crafting durable, electrically insulating components in EV battery systems. Bossard's grasp of design optimization rules allowed it to propose solutions for embedded fasteners without constant guidance from injection molders, streamlining communication between design and manufacturing stakeholders. Understanding how fasteners interact with these materials, including pull-out and over-torque resistance, ensured optimal performance in the proposed designs.
Need for tailored standard insert studs for manufacturing
In traditional mold setups, external thread mechanisms secure insert studs. However, space limitations in this case ruled out such methods, risking unsecured inserts during molding. To counter this, Bossard worked with tooling engineers to integrate a core pin retention geometry into the insert stud design, a solution, that is compatible with standard practices.
Meeting assembly loadability expecations
Ensuring assembly loadability is crucial for maintaining torque callouts, like those for PC8.8 or PC10.9 fasteners. Simply enlarging the fastener wasn't feasible due to constraints. Adding thickness risked violating anti-arcing requirements (A), while increasing diameter could compromise neighboring components (B).
Bossard addressed this challenge by patenting knurling designs, optimizing engagement with the polymer. Finite element techniques validated mechanical performance, while CAD data sharing expedited clearance checks. Continuous communication with tooling engineers ensured pin geometry feasibility.
Customer benefits at a glance
- Faster time to market:
Bossard was able to save time and resources by guiding the design process, avoiding trial and error.
- Optimized manufacturing setup:
The technical solution helped to avoid costs related to tooling damage, scrapped molded parts and product recalls.
- Single point of contact:
Bossard’s design expertise aided in defining relevant requirements and then ensuring the designs met these.
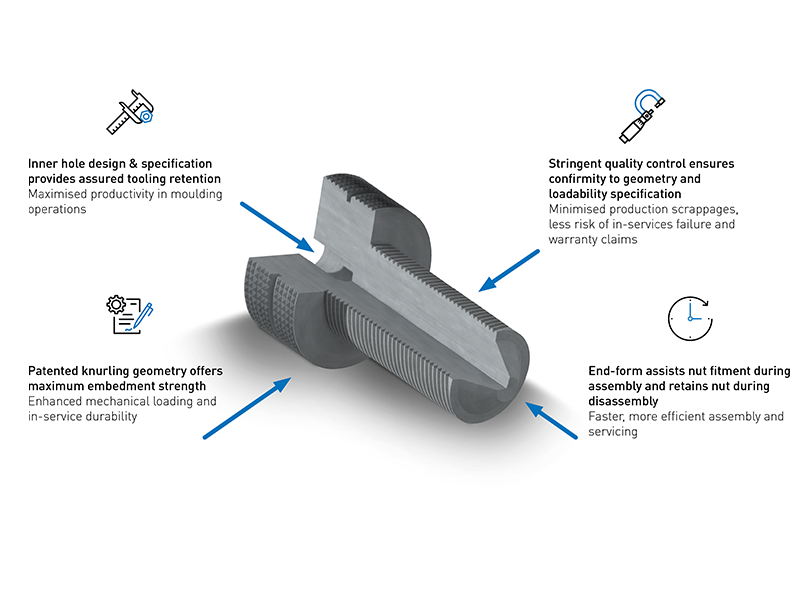
Find out more about our Expert Design service