Replenishment of parts
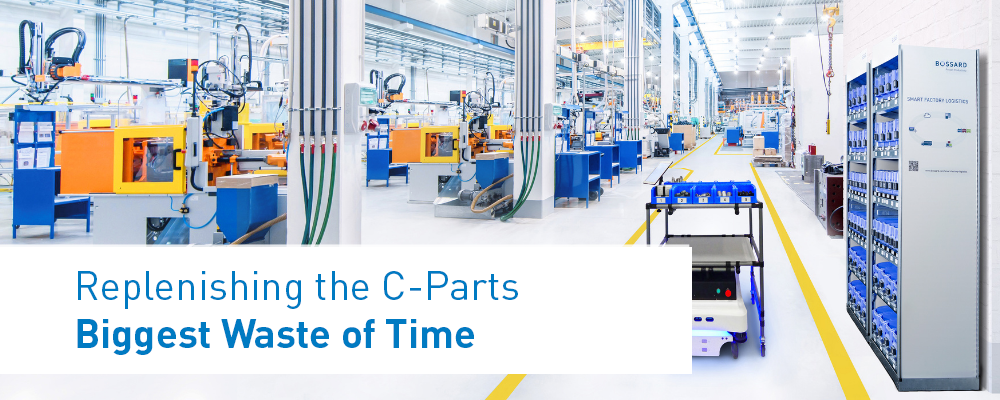
Moving parts around in production is costly because it takes time. When handling C-parts in the manufacturing process, time wastage is the biggest enemy, as every extra movement of these items in the warehouse or on the production floor increases the total cost of ownership (TCO). Therefore, it is important to automate the replenishment process as much as possible to keep costs down - from the moment an item arrives until it is replenished on the assembly line.
Without automated replenishment: lower efficiency, higher costs
In Company A's production, the assembly area must be replenished daily with new stocks of parts from the central warehouse. The person responsible for the internal distribution of these parts goes around the production floor and checks one line at a time, noting which items are missing from the lines. The central warehouse then has to locate the items in the long shelf aisles at designated locations. He usually knows what is used roughly daily, fills his cart with goods and after a while returns to the assembly lines to fill in the missing items.
However, there has been a change in production in Hall 1, and by the time the operator arrives, not all the correct components are available for that assembly. Hall 2 needs the missing parts immediately, otherwise production cannot start. In one of the assembly lines, the wrong part number was filled in when recording the missing items. Upon returning to the central warehouse, an internal distribution worker cannot find the location of the new items because they were misplaced on the warehouse shelf. After locating the new items, he must now deviate from the normal replenishment route and decide which route is the fastest so that production does not stop. Such misunderstandings and mistakes can be repeated every day.
Summary: Time loss increases with every move back and forth between the central warehouse and the point of consumption.
Time is lost when the operator does not have up-to-date digital data,
- where the item is physically located in the central warehouse,
- where it needs to be replenished,
- which workstations need the items first
- and which replenishment route is most optimal
With automatic refilling
Now, let's describe a situation where automatic ordering is available for replenishing items. After checking the inventory, the assembler of company B sends a request for replenishment of parts directly from the assembly station by pressing a button on the digital label of the storage box. This information is automatically sent to the responsible employee in the mobile app in the form of a digital list.
The internal distribution manager can see on his mobile device which items need to be delivered from the central warehouse to the assembly lines. In the central warehouse rack, the LEDs on the boxes from which the goods need to be picked flash one by one. Once picked, they can see on their mobile device the optimum possible route for replenishing the items on each production line, allowing faster replenishment without unnecessary wandering. In the final step, the operator arrives at the production lines, where successively lit LEDs on the storage boxes indicate where to replenish a particular item.
Summary: Automated replenishment eliminates unnecessary delays in checking and replenishing missing items.
Technology contributes to the efficient processing of time-consuming steps in production, saving time and minimizing unnecessary movements with up-to-date inventory visibility.
Stay tuned to learn about how to prevent time wasted in purchasing, manufacturing and C-parts warehousing, such as internal ordering, external ordering and how to automatically track inventory levels and missing items.