How to Eliminate Wasted Movement in Your Factory with Last Mile Management
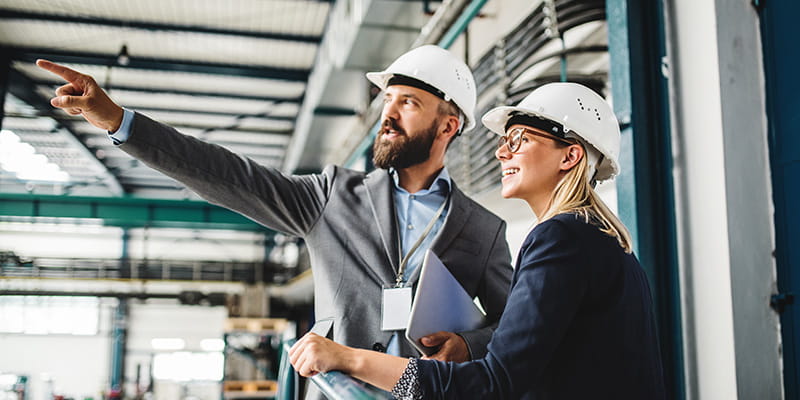
Production is complex, and there are a multitude of ways that things can go wrong. A single part can move through many hands and be relocated across many work areas before it becomes a completed product. Parts and incomplete products can be damaged, mis-directed, and lost during this process.
However, today’s workplaces are more demanding than ever before. The fourth industrial revolution demands that parts be located quickly, transported automatically, and shipped on time, all while being instantly tracked in the cloud. Decreasing wasted movements and minimizing human interaction are key components of today’s smart factories.
Because of today’s smart solutions, supply chain and material handling processes can become faster than ever, meeting and exceeding expectations. With the correct solutions, your factory’s B- and C-parts can be managed in a way that gets your products to end users efficiently and transparently.
SmartBins and SmartLabels
Properly identifying, handling, and replenishing parts is crucial to material flow. Bossard’s SmartBin and SmartLabel technology not only tracks parts throughout the supply chain, but also automatically triggers demand requests to keep workers in place. Quantities are sent and received as needed while movements and errors are reduced.
All data is stored within a cloud-based system that communicates instantly to mobile devices like tablets and smartphones. All stakeholders can quickly access information, reconfigure workstations, and collaborate to overcome obstacles. Taking this concept one step further, crucial inventory can be replenished and then seamlessly moved by robotics across the shop floor.
Autonomous Mobile Robots (AMR)
Bossard’s Last Mile Management software fully connects SmartLabels and SmartBins with autonomous mobile robots (AMR) to bridge the gap between big-data and automation. Each time a part moves, the chance for error increases. Allowing robotics to move parts from one area of the job floor to another produces the following benefits:
- The most efficient route will be taken.
- Workers remain fully engaged in manufacturing.
- Obstacles will be avoided.
Automated mobile robots can move throughout the manufacturing space 24/7. They avoid obstacles, open doors and gates, and can even ride elevators. They do so at the most efficient pace on the most efficient route. They are incredibly useful in ever-changing spaces where conveyor belts are not as effective and can be controlled remotely. Modifications are made on demand with a constant flow of materials.
Remote Dashboards
Before the on-set of Industry 4.0, inventory levels and the supply chain existed in a void. Executives lacked visibility to make quick business decisions and it was difficult to mitigate risks and improve lead times. This lack of transparency created silos of information and forced executive decision-making to be reactive, instead of proactive. It was hard to anticipate scenarios, resolve issues, and include all stakeholders in the process. Executives relied on cumbersome reporting generated by workers, which were often drags on production.
With emergent smart factory technologies and big data being transferred to the cloud, managers and customers can optimize material flow from remote locations. Working from a single view of the supply chain eliminates inefficient processes and reduces the number of people in work areas. Less human interaction means fewer chances for errors, fewer obstacles lineside, and fewer workplace movements. The long-term time-saving factor of bringing decision-makers closer to production is exponential.
Bossard’s Smart Factory Logistics and Last Mile Management allow for better, leaner and smarter operations. Contact us today to learn more or to schedule a consultation.