The customer: a market leader in hydrant technology
The Swiss company Hinni AG offers services in the field of hydrant control maintenance and revision. In addition to hydrant bases and tops, the company produces various spare parts and accessories for the hydrant models commonly used in Switzerland. Continuous service orientation and power of innovation made Hinni the market and technology leader in these areas.
The product: high-quality water hydrants
About one meter tall and known for their often bright-red look, hydrants are indispensable in disaster situations. Besides supplying the fire department with water in case of emergency, hydrants also serve a number of other purposes, such as supplying water for street cleaning and construction sites or playing a role in the maintenance of pipes.
Demanding requirements
Hydrants need to withstand different environmental impacts in these various applications, and they are usually in use for up to 50 years. Therefore, sturdy high-quality materials are used during production. The disadvantage that comes with this: Depending on the design, hydrants weigh between 30 and 60 kilograms.
The challenge: handling the heavy hydrants safely and efficiently
Due to the heavy weight of the product, special measures are taken when assembling and installing hydrants. The fitters use cranes or similar lifting aids in order to prevent health problems, such as chronic back pain.
This process, however, comes with its own challenges: moving the hydrant blanks from point A to point B within production can be cumbersome and take a lot of time. Hinni was looking for a simple solution to this problem.
Our simple solution: threaded lifting pins for ease of use
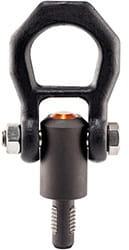
When Bossard was brought in to solve this challenging situation, we came up with a surprisingly simple and practical suggestion: self-locking, steel M16 threaded lifting pins.
- They possess a movable shackle, which makes it possible to easily attach them to a crane hook.
- The threaded lifting pin can be inserted into the thread of the cast iron blank at the simple push of a button. No time-consuming screwing in and out is required.
In this way, the blank can easily be lifted using the crane and positioned as desired. Removing the threaded lifting pin again just takes a push of the button.
This solution completely convinced the customer. The Hinni fitters were excited by the simplicity of use and the time savings it could allow: “Using the threaded lifting pin helped us out tremendously – we are super happy with Bossard’s solution.”