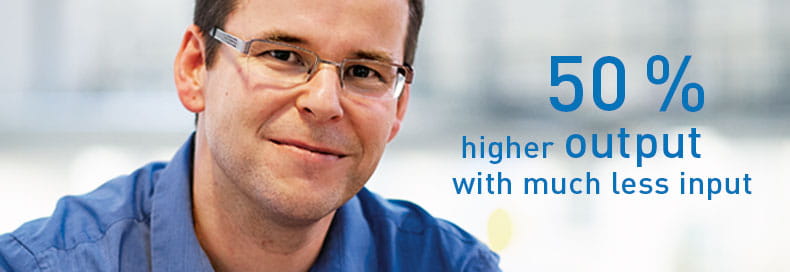
Willi Bühlmann, Project Manager, Production, Siemens Building Technologies Division, Switzerland
"Our partnership with Bossard is key to our success."
The Siemens Building Technologies Division is a global leader in building automation. Its innovative product portfolio of TX/IO modules is a noteworthy example of the division‘s work, combining sophisticated technology, elegant design and simple engineering to control building processes from shade to lighting. Building Technologies now produces around 410 000 of these control modules annually.
Capacity limitations manifest themselves in system failures
As project manager I was tasked in 2009 with optimizing production performance of the TX/IO modules, including the assembly system. This was absolutely necessary, as the production process itself was susceptible to problems, while demand was rising. This had taken our assembly system up to its capacity limit, which was evident in the
system errors encountered, up to 150 daily.
An analysis revealed that the screws were the main cause of the problems. The TX/IO modules – each with 16 to 32 screws depending on module type – are installed into the corresponding socket. This process is carried out automatically by a screw system which is part of a robot cell. Screws that are too small, too large or otherwise defective were causing system problems and production stops involving extra work and assembly delays. Numerous complaints with the former supplier and having to sort out foreign parts created a lot of additional quality assurance work as well.
Custom-made screws and new assortment
Having a background in mechanical engineering, I was well familiar with “Bossard Fasteners”. So I thought it would be a good idea to contact Bossard technical associate Albert Schibig for help. Three days later a Bossard team arrived at our production facility in Zug to gauge the problem. The Bossard professionals came to the same conclusion I had: “These screws are definitely a problem.” The next steps were discussed that same day and a plan of action drawn up. Just a few weeks later I had custom-made sample screws and an offer for 6 million slotted screws annually on my desk. The price was right, the quality was excellent, and the trials were successful. In addition, our TX/IO product manager was able to get a customer request accommodated. They increasingly demanded for crossed slot screws. This was no problem for Bossard, who shortly thereafter delivered screws of the desired variety. The Bossard team advised us as well on designing a new screw machine system. Working with Bossard enabled us a substantial overall gain in productivity and process reliability; the added value is quite clear.
Yet optimization of the assembly system was only part of the project. After a number of other strategic measures implemented along the entire value chain of the overall TX/IO project, this product range is now considered a “lean” reference at the production site in Zug. Bossard played a significant role in our ability today to produce 1 500 to 1 800 modules per day in two shifts, in contrast to 1 000 modules in three shifts as used to be the case, corresponding to a productivity increase of more than 50 %.
Ref. BOS-AE-EL-00714