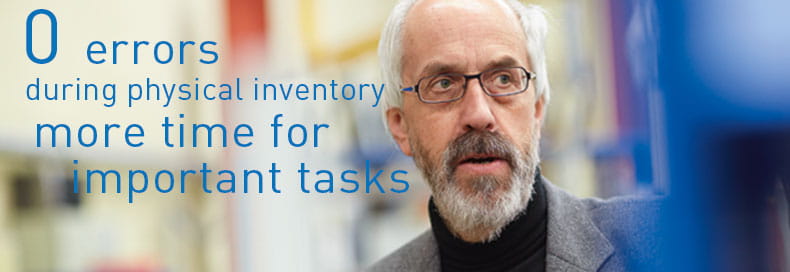
Hans Frehner, Production Manager, TROX HESCO Schweiz AG, Switzerland
“How to liquidate your central warehouse while still saving money”
20 years ago, hardly anybody talked about kaizen, the Japanese philosophy of life and work which focuses on continuous improvement. When I started my job as the purchasing manager of what at the time was Hesco, my first project was to make our logistics processes more efficient.
Screws and other fastening elements were stored in a large warehouse located at quite a distance from production. Not only was this a relatively expensive storage location, it was also easy for employees to help themselves to whatever they needed, which made it difficult to keep track of the inventory.
Availability of fasteners was greatly simplified
As far as screws and other fastening elements were concerned, I’d already had a very positive experience with Bossard, which at the time was run by Heinrich Bossard. Therefore, the first step of my project to improve the efficiency of our logistical operations was to introduce the two-bin system. This change required a great deal of commitment from everybody involved. A few years later, we introduced the Bossard SmartBin system, an automated procurement process where orders for C-parts are automatically triggered by weight sensors. The switch from a central warehouse to SmartBin had a positive effect on the entire production because the availability of fasteners was greatly simplified. Physical inventory also became much easier because with this system we receive the inventory figures directly from Bossard. For many years now we’ve been able to finish the physical inventory of our small parts storage with zero errors.
Greater efficiency and flexibility
As part of the Kaizen philosophy of life and work that I mentioned earlier, we set up production islands to improve our workflows even more. In the production island where fire dampers are made, there is a storage area for semi-finished products which we call “the supermarket.” A warehouse worker fills “shopping carts” with everything that is needed to manufacture a fire damper and then makes these components available to the assembly workers. We operate according to the one-piece flow principle. Not only does this make us more efficient, it also allows us to address the requests of our customers more flexibly and to interrupt production at any time if another, more urgent job requires it.
The original warehouse isn’t needed any more. Today we rent it out, which gives us additional revenue.
As the production manager, I want my employees to work efficiently right where the value of our products is created. This means that we eliminate any waste, such as unnecessary transport routes. Value stream analysis and SmartBin flex are additional projects we plan on tackling in cooperation with Bossard.
Ref. BOS-CL-FM-01214